
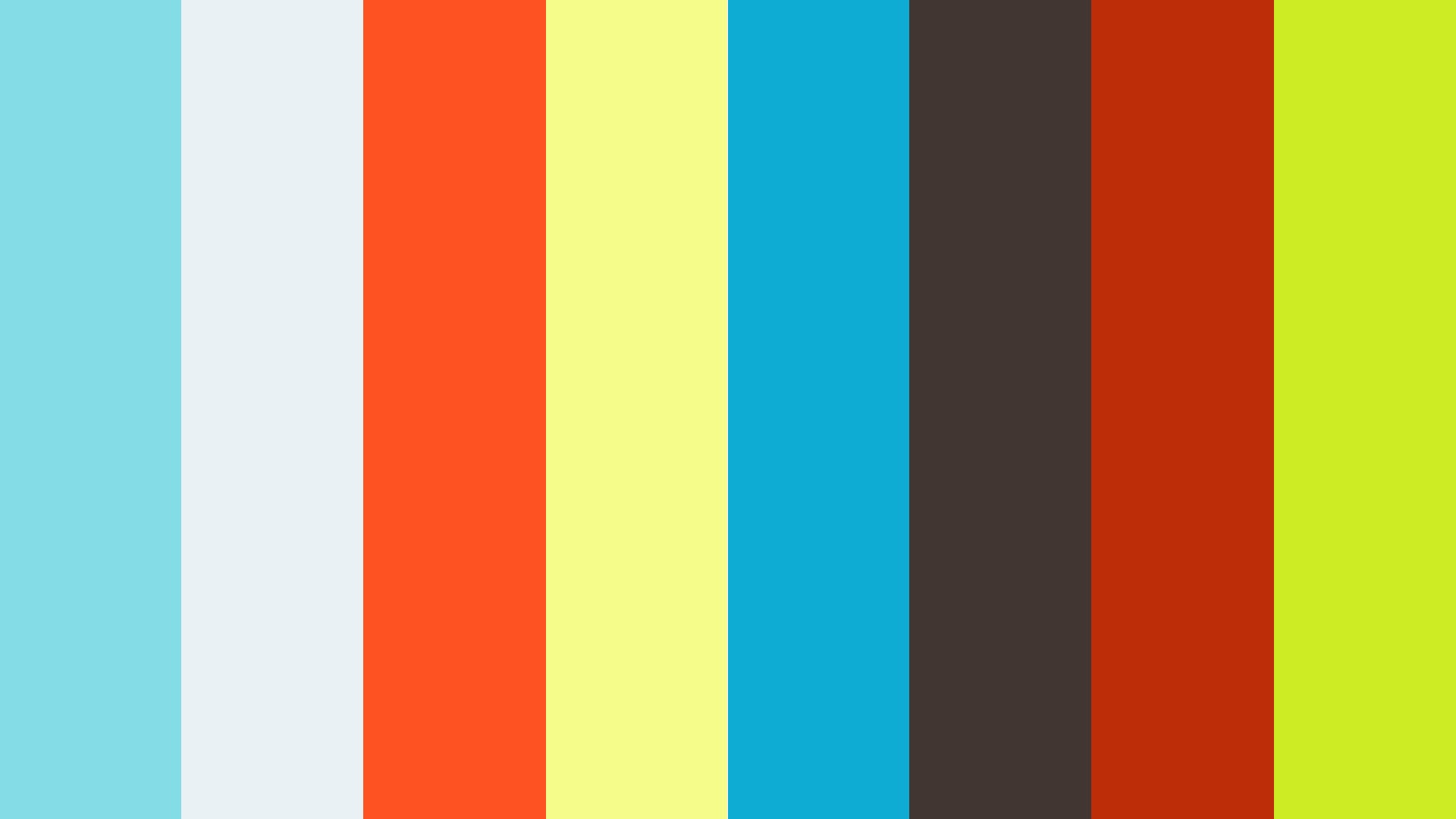
- #Mastercam 2019 undercut surfaces drivers
- #Mastercam 2019 undercut surfaces full
- #Mastercam 2019 undercut surfaces windows 10
- #Mastercam 2019 undercut surfaces pro
- #Mastercam 2019 undercut surfaces software
#Mastercam 2019 undercut surfaces drivers
Make sure you are using up-to-date drivers from your card manufacturer. These do not generally have the capability to drive graphics intensive applications such as Mastercam. We do not recommend or support the use of onboard graphics found with some PC configurations. OpenCL is required for Mastercam to be able to hand off certain computation tasks to the graphics card to increase system performance.
#Mastercam 2019 undercut surfaces full
Other graphics cards can be used, but they must offer full OpenGL 3.2 and OpenCL 1.2 support.
#Mastercam 2019 undercut surfaces pro
We recommend an NVIDIA Quadro® or AMD FirePro™ / Radeon Pro card with 4 GB or more of memory. When purchasing a new computer for Mastercam, one of the most important component is the video card. For large toolpath generation and simulation, we recommend 32 GB of RAM. When Mastercam uses all available RAM, it switches to using virtual memory space, which is stored on the hard drive, and will dramatically slow the system down. We typically see a 50% reduction in toolpath calculation time with the latest Intel i7 or Xeon processors. Toolpath calculation and Simulation will generally run faster with a multi-core processor. With each release, more and more aspects of Mastercam are becoming multi-core processor aware.
#Mastercam 2019 undercut surfaces software
The processor speed will impact how fast the software will calculate and complete tasks. Mastercam X7 MU2 was the last release to support Windows 7 32-bit OS. While Mastercam may run on other Windows editions (such as Home Edition) or virtual environments (such as Parallels for Mac), it has not been tested on these configurations and is therefore not supported.
#Mastercam 2019 undercut surfaces windows 10
We recommend using Windows 10 64-bit Professional editions. continues to review the operating system (OS) requirements for Mastercam with a goal of providing the best possible user experience for our customers. View Detailed Requirements And Suggestions OPERATING SYSTEMSĬNC Software, Inc.
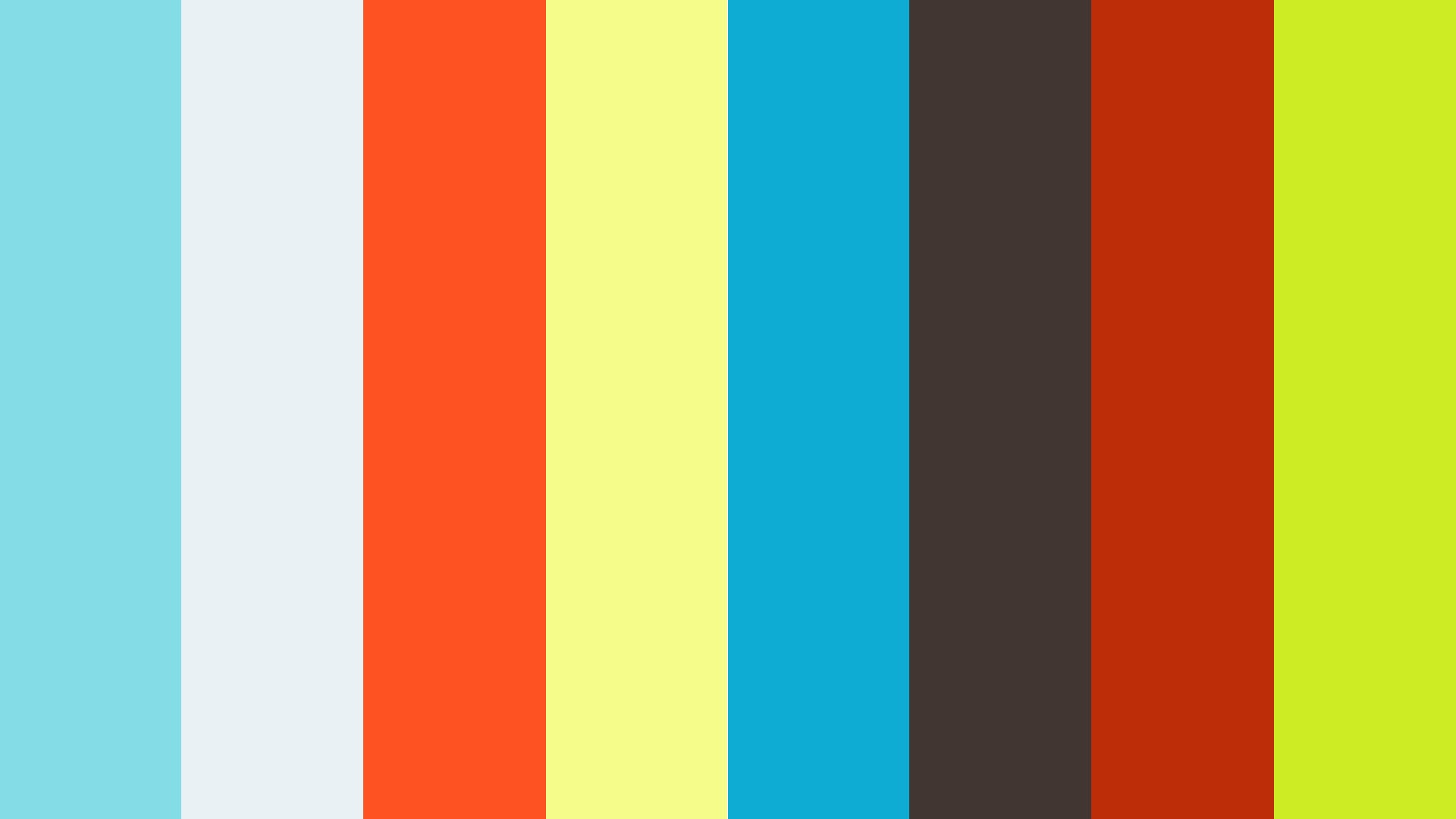
The maximum cutting area of the Roland CNC router is 19.68in (X) x 15.74in (Y) x 6.10in (Z).

RhinoCAM is a plug‐in that is available in the computer labs. Parts to be CNC machined must be programmed using RhinoCAM, MasterCAM and other programs can be utilized but the CLT must run the gcode to make sure the program will work on the machines. The following is a list, by no means all‐inclusive, of some basic guidelines to keep in mind when designing parts to be fabricated by CNC machining: Though they vary widely, a typical CNC cutting strategy would include profiling, roughing, semi‐finishing, and finishing passes. End mills cut along tool paths with specified linear feeds (typically measured in inches of movement per minute or in/min) and rotational speeds (typically measured in revolutions per minutes or RPC) that are determined by the cutting strategy being utilized, the size and type of the tool, and the material being machined. Though CNC machines come in a variety of forms, most are capable of simultaneous 3‐axis movement with X and Y motion controlled by the gantry and Z motion controlled by the spindle head.
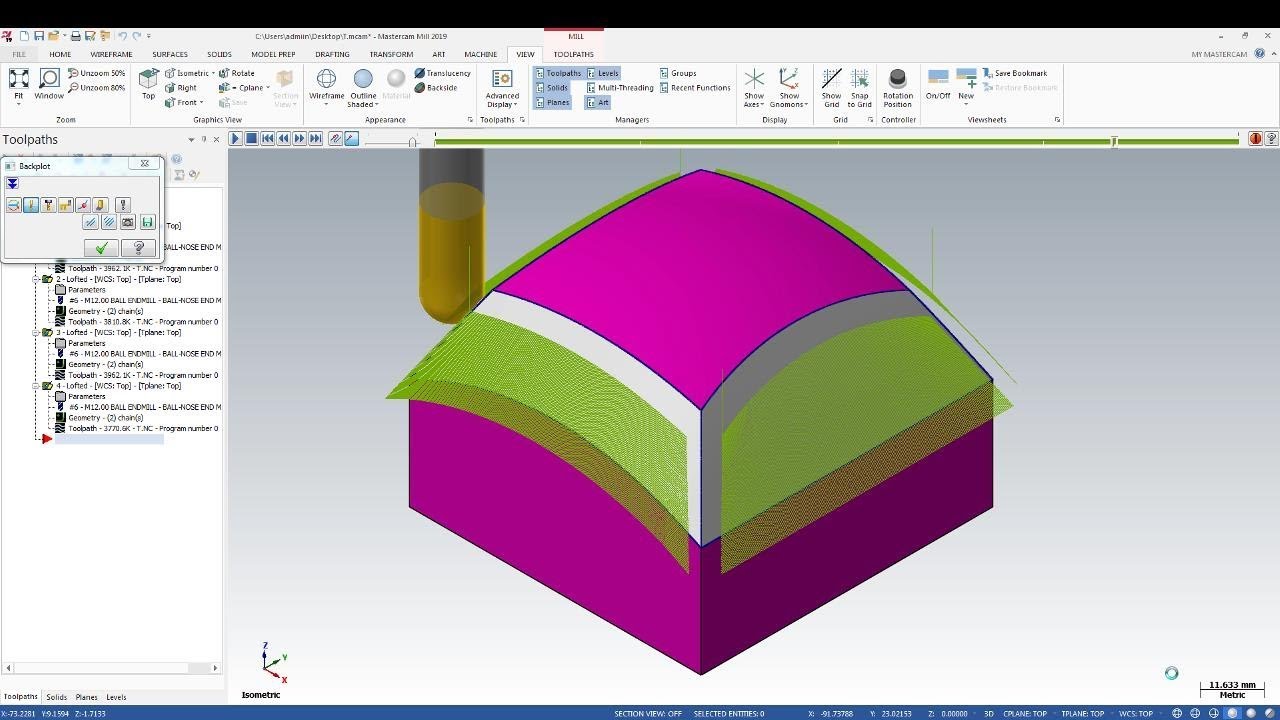
CNC machining is a subtractive fabrication technology that uses a computer numerically controlled cutting tool (end mill) to “carve” design prototypes from a variety of sheets or blocks of material including foams, woods, plastics, and metals.
